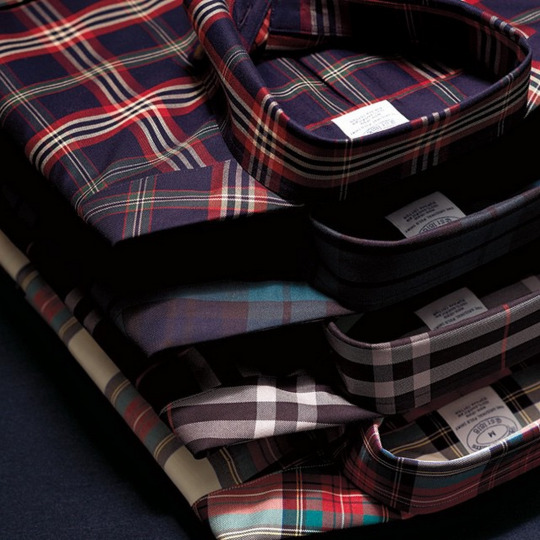
Brooks Brothers just started their Friends & Family sale. The event used to be held mid-season, but it’s apparently gone pre-season now (aren’t we technically still in summer?). In any case, you can take 25% off almost everything on their site with the checkout code FRIENDS. Some notable items include:
- Boots: These shell cordovan boots are some of my favorite shoes to wear with both jeans and tailored trousers. They also come in a suede version, which you can spray with a waterproofer and turn into rain boots.
- Slip-Ons: Some nice models for tassels and pennies. Also a lightweight tie model from Crockett & Jones (available in pebbled grain or suede), which I think go well with casual suits.
- Unstructured Shoes: Floppy, unstructured bluchers and chukkas from Alden.
- Edward Green: Surprisingly, certain models from Edward Green work with the discount code, such as the Bordon bluchers, Newmarket Chelesas, and Longmoor wingtips.
- Outerwear: Some Beretta hunting coats, starting at about $300 with the discount. This model has a shoulder strap system inside that allows you to sling the jacket across your back when it’s not in use.
- Shirts: The coupon code stacks on Brooks Brothers’ Every Day Value deals, which means shirts come out to about $57 apiece if you buy in sets of three. Check out their oxford-down button-downs (available in both solid-colored and striped options), as well as dressier chambray and denim models.
- Luggage: Brooks Brothers’ sales are always the best time to pick up Filson bags. They also have a good range of luggage from JW Hulme, if you want something in leather.
- Accessories: There are some nice things here and there if you browse the accessories section. I’ve always liked Brooks Brothers’ tartan umbrellas for their value, as well as some of their dress belts (I use this model). Also worth checking out are the gloves, scarves, garment brushes, shoehorns, tie cases, and dopp kits. My favorite item is this Lock & Co sisal hat. I bought one last year and have been wearing it all summer long.
- Sale Section: There are some linen shirts in sale section that come down to an appreciably low $45 with the discount code. Available in both solid colors and stripes.