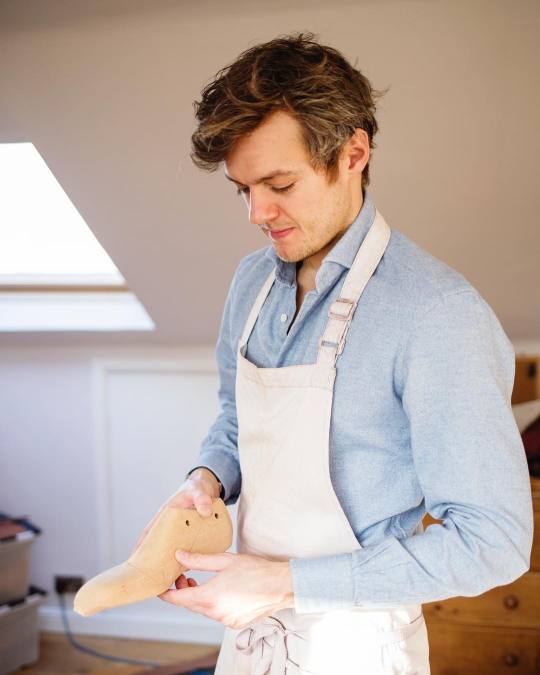
John Lobb’s shoemaking workshop on St. James of London looks like an old university office. Harsh florescent bulbs hang overhead, casting light upon leather armchairs, glass showcases, and dusty objects left untouched. The shop feels fusty and cluttered. Thick, ancient ledgers stretch across the shelves that run high and around the back offices. Racks are covered deep with wooden lasts, which are arranged in no apparent order. In a BBC documentary, Brian Dobbs, who wrote a book on the firm’s history fifty years ago, climbs a stepladder to retrieve one of Lobb’s archives. “Well the shelves weren’t arranged for historians, that’s for sure,” he says wryly. “This is less archaeology and more mountaineering.” As he tries to take the book down, a bundle of wood tumbles off the shelf below, clanking onto the floor.
John Lobb’s building is much larger that one might imagine for a shoemaking firm that produces 500 pairs of bespoke shoes per year. Before the 1950s, this space housed a Rolls Royce dealership. Towards the back, a lift carried fancy cars up and down between the floors for visitors in the showroom. The Lobb family moved in after their old premises were destroyed during the Second World War. Today, lastmakers on the ground floor carve made-to-measure lasts from roughly turned blocks, and three flights down lead to additional workrooms. The shop is big and somewhat quiet, animating Thomas Caryle’s observation that “a man cannot make a pair of shoes rightly unless he does it in a devout manner.”
If you walk down those stairs today, you’ll be flanked by stacks of shoeboxes, each containing a pair of handmade shoes. Some of those are customers’ orders ready to be collected; others are apprentice projects; and others still are forgotten shoes left unclaimed. For whatever reason, whether sudden death or unforeseen poverty or simple forgetfulness, many people fail to claim their shoes after ordering. On the upside, if you can make it to John Lobb’s workshop in London, that means you can purchase bespoke shoes – made to someone else’s measurements – at half price. Nicholas Templeman, who worked as a lastmaker at John Lobb for seven years before starting his own bespoke shoemaking firm, used to fetch those shoes for people hoping to test their fortunes. “To be honest, it rarely works out,” he says. “It’s not like pulling a pair of ready-to-wear shoes off a shelf and trying a size 8. These are all made for someone, so all their idiosyncrasies are built into their last. Every now and again, however, someone gets lucky.”
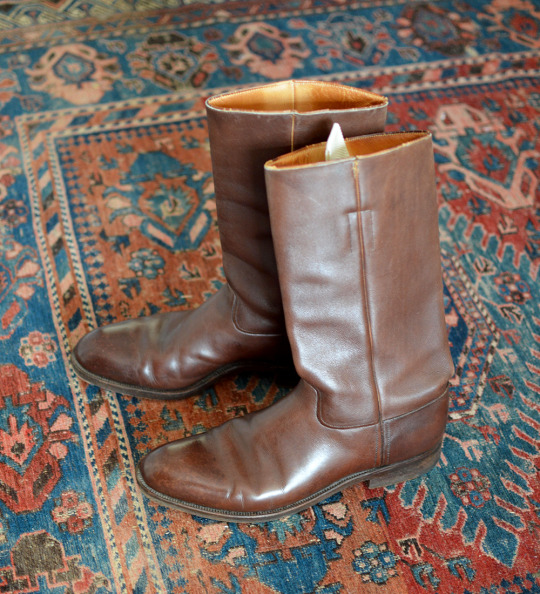
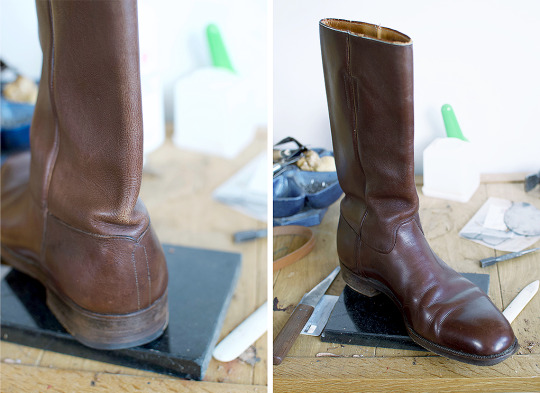
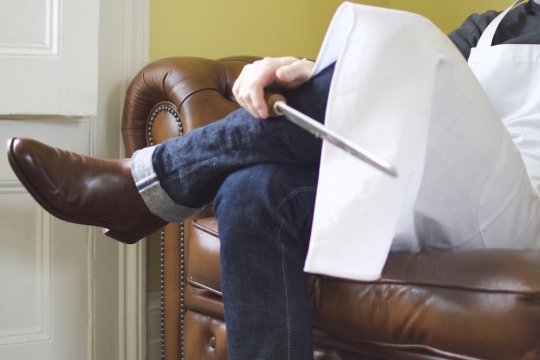
Luck comes more easily when you’re a bespoke shoemaker. During his first few years at Lobb, Nicholas found a pair of military boots hidden amongst the stack of unclaimed footwear. They’re half-Wellingtons, which are named so because they’re made with four pieces of leather, rather than the two pieces that define a full-Wellington. The boots initially fit well along the length and around the calf, but they were a half-inch too wide, leaving them too loose to wear. So Nicholas unstitched the soles from their uppers, relasted them according to his last, and put them back together again. Thirty years after they were originally made, they’ve found new life in Nicholas’ closet. He pairs them with a grey herringbone tweed from Sartoria Solito, a sea-green chambray shirt from Simone Abbarchi, and slim-tapered jeans from Iron Heart (it’s the same outfit you see here). The boots are an excellent way to dress down a tailored jacket, and on occasion, he wears them with a recently acquired Aero Board Racer.
Since every story about bespoke shoemaking sounds like it was lifted from a Dickens novel, it’s easy to forget how many casual styles are often made in the back of these workshops. Nicholas’ boots are a good example of the kind of shoes that can be worn with modern tweeds and trim leather jackets, but are still made to the best of West End standards. Back when he worked at Lobb, Nicholas carved lasts for horsebit loafers, cowboy boots, elasticated Chelsea boots, side-zip boots, and some more unusual designs.
Amanda Palmer, who sings for the punk-cabaret duo The Dresden Dolls, once ordered a pair of platform boots that one can only assume were meant to be worn on stage. They’re tall and towering, with a line of Victorian-style buttons going down the front, but a side zipper for easier entry. Tom Cruise, similarly, once ordered six pairs of German military boots for his role in Valkyrie (Nicholas carved the last for those, but I was unable to get him to confirm or deny that Cruise wore a prosthetic butt in the film). Why would anyone need six pairs of the same boot when leather shoes only get more comfortable with wear? “I don’t know,” Nicholas says. “But for his following role, I think in a Mission Impossible film, he ordered something like sixteen pairs of the same derby.”
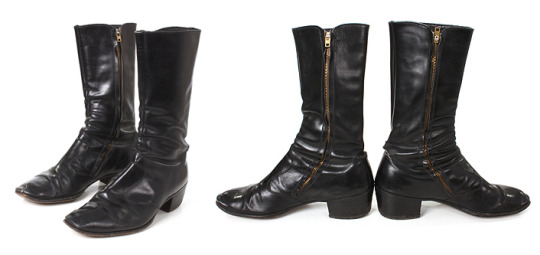
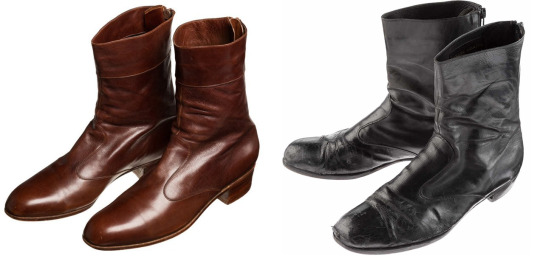
Nicholas, who once made a pair of Alden Indy styled boots for a customer, says almost anything is possible through bespoke. The most critical aspect of fit is the heel-to-ball measurement, but the rest of the design can be made however the customer likes. “You can lose some of the benefits of bespoke, such as better arch support, once you cut things a little further from the foot,” he says, “But for more casual styles, the upside is that you get the best craft methods. So long as the uppers are in good shape, you can relast them as many times as you want. With machine-welted shoes, unless you’re taking extreme care, re-welting will generally leave new holes since the machine will punch holes where it wants. But with a hand-welted shoe, you can reuse the same holes, and replace things such as insoles, which means shoes can last a lifetime. At Lobb, we got 50-year-old shoes back all the time for recrafting.”
Some of my favorite examples of bespoke casual shoes were made for Frank Sinatra. The tall, zippered boots you see above were custom-made for the skinny, blue-eyed singer from Hoboken during 1970s and ‘80s. Sinatra wore them with dark suits and tuxedos while singing uptempo hits such as “New York, New York.” And not that Sinatra needed any help, but the boots were often made with a Cuban heel to give him some dramatic stage presence (Sammy Davis Jr. and James Brown wore the same style when performing). The black side-zip ones would later be given as a gift to Michael Castellano, Sinatra’s personal friend and “right-hand man,” for his services. At the 10:30 mark of this BBC documentary on British professions, you can see a young Bill Bird at Peens, a tree-making operation once owned by John Lobb. Bird is failing to be discreet about their famous customer as he shows off Sinatra’s lasts.
Prince also famously had bespoke shoes made – more than 3,000 pairs (3,000!!) during his lifetime to fit his glam-god ensembles. Most of those commissions were for heeled booties that he liked to wear on stage, at home, and everywhere in-between, but he also had platform flip-flops for lounging. The boots were specially produced with a stainless steel bar to ensure the heels wouldn’t snap off during his intense performances. At one point, the performer asked his shoemaker, Andre Rostomyan, to produce a purple velvet version of his favorite boot style. Since Prince had his own shade of purple, however, the fabric had to be custom woven in England. Vogue writes of the collection:
Prince maneuvered better in his high heels than most stiletto-clad women do. He would do the splits, jump up, high kick, squat, and run back and forth onstage with specially built 4-inch and 3 1/3-inch height boosters at his soles. After all, Prince Rogers Nelson was a man of mega-talent and charisma but was also of diminutive size. He was famously 5-foot-3 and chose to wear heels to lift himself up a bit, though he certainly didn’t need it. Prince also once said that he liked to wear heels because women were attracted to them – and why not? His aura was a regal, ethereal, sexed-up shade of purple, and his style had to match all of that pomp.
“At one point, we were averaging 30 to 40 pairs of shoes a month for Prince,” Gary says. “I think he must have worn at least two or three of those shoes a day because he refused to be seen at, say, a press conference in the morning wearing the same heels as he wore onstage the night before.” Though most of the design consultations were done over the phone and by mail, Prince did visit Andre No. 1 a few times when he was in Los Angeles. “He was very much involved in the process,” Gary says. “Prince would get attached to a certain fabric and bring it in to me and ask, ‘Okay, how can we cut this? Do we do it on the bias?’ He really dug into the process.”
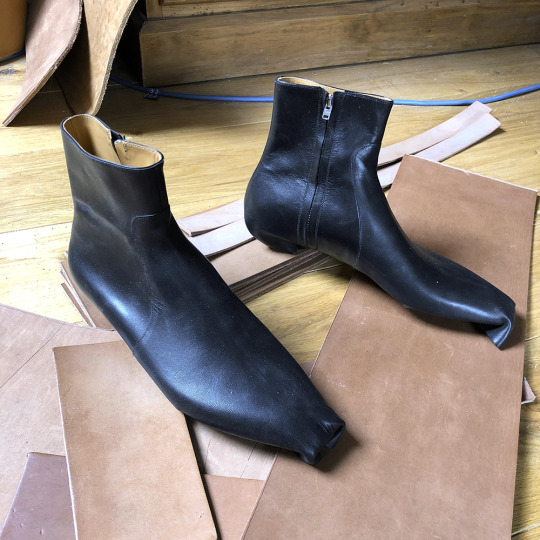
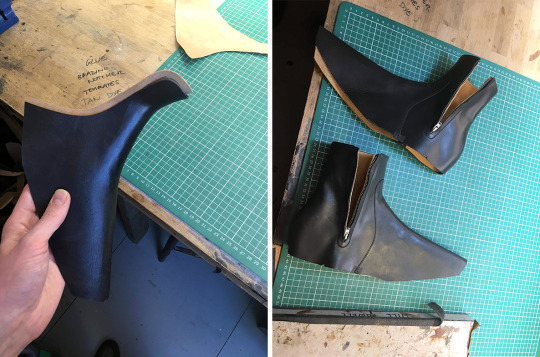
I’m currently on my fourth pair of bespoke shoes (third pair with Nicholas). They’re black side-zips designed to replace a pair of Margielas I often wear with black jeans, black leather jackets, and charcoal topcoats. They’re pictured above in their current half-made stage and look a little sleeker than normal because the soles haven’t been attached. Once finished, their toe shape will look close to Nicholas’ half-Wellingtons.
Nicholas is one of the best bespoke makers I’ve had the pleasure of working with. At larger firms, ordering clothes can sometimes feel more like a made-to-order process. You choose your material and details, and then come back a few months later for a fitting. In the end, you get some customized version of a wingtip or patch-pocketed sport coat, but it’s usually in the company’s house style.
With Nicholas, it’s easier to work out everything from the exact toe shape to stitching details to finishing. Nothing has to be communicated through an intermediary salesperson and he’s always available for a chat on the phone. It’s been easier to get personal attention this way and figure out smaller details together, whereas I think it would be a struggle — if not, at least, feel like an embarrassing bother — if you did this at a larger firm. Years ago, when I ordered my first pair of bespoke shoes, I asked a friend with a lot of experience in this field who I should go with. “Nicholas will give you a lot more attention, so the process will feel easier and smoother,” he said. I think he was right. This difference is even more important when you stray into more casual styles, which may deviate from the standard dress shoe templates.
Nicholas is touring the United States again this spring. Trunk shows are scheduled in Washington DC, New York City, and San Francisco from April 30th until May 5th. If you’re interested in ordering, or perhaps just want to see his work in person, you can schedule an appointment through his website. Bespoke shoes don’t have to be just about black cap-toe oxfords and formal wingtips. In skilled hands, they can be better versions of your favorite casual styles. And while they won’t transform you into a Prince or Frank Sinatra, they do kind of make you feel like one.
(photos via Nicholas Templeman, Dapper Made, Maslow So, Shoegazing, The Golden Closet, Heritage Auctions, and Vogue)
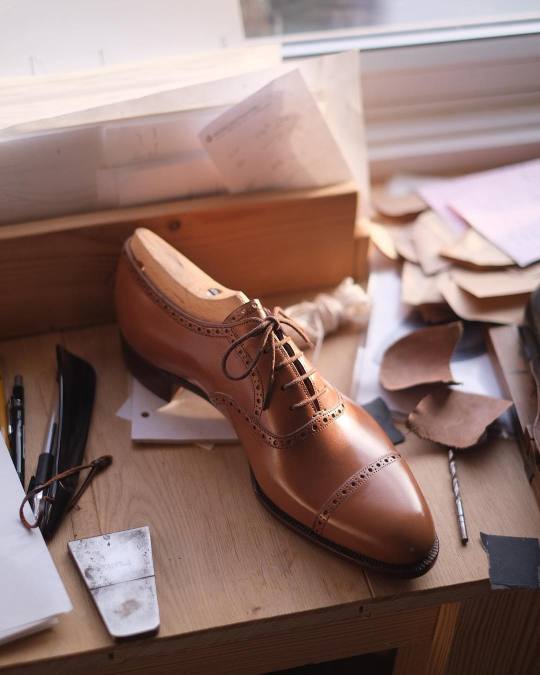
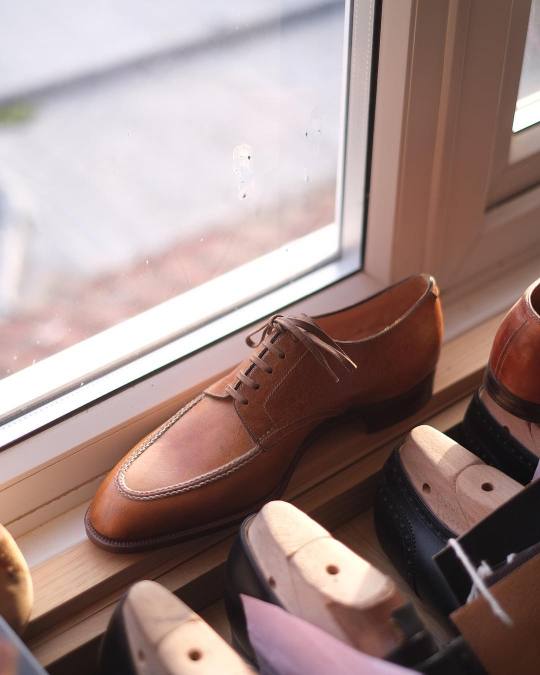
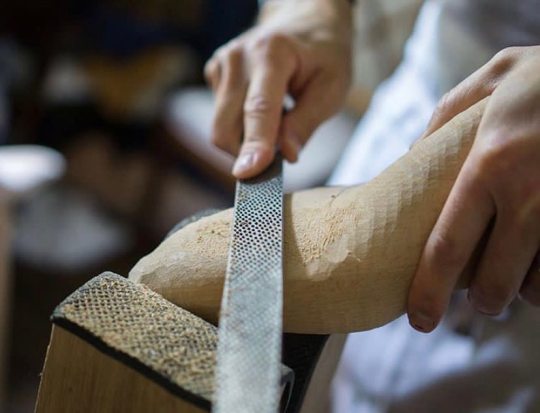
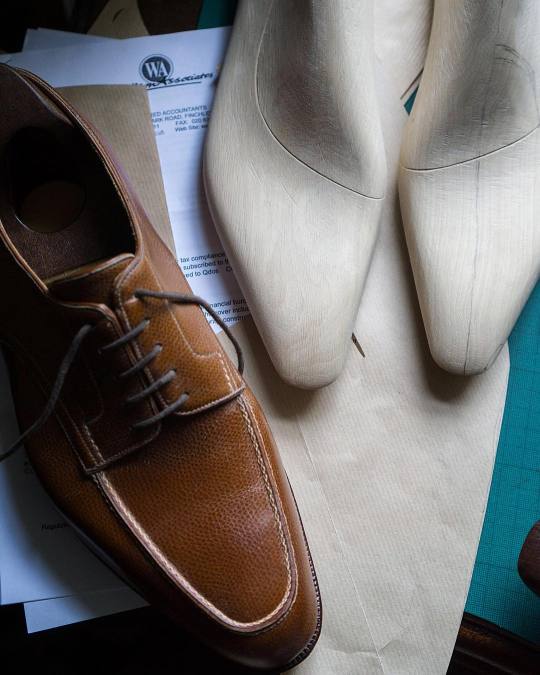
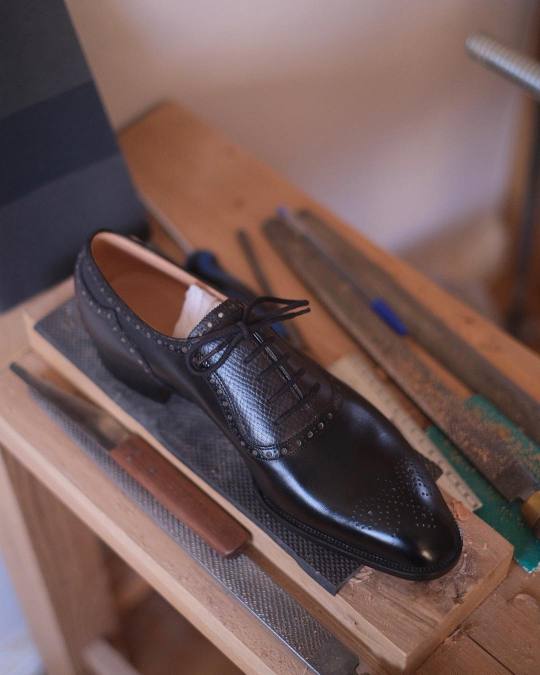
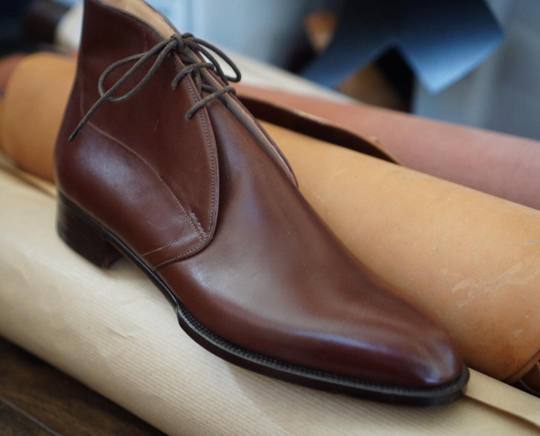
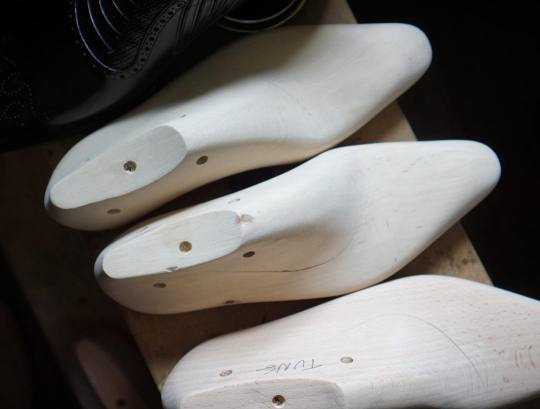
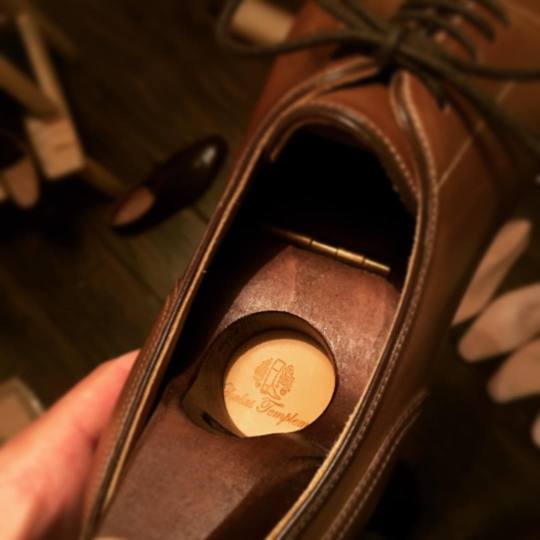
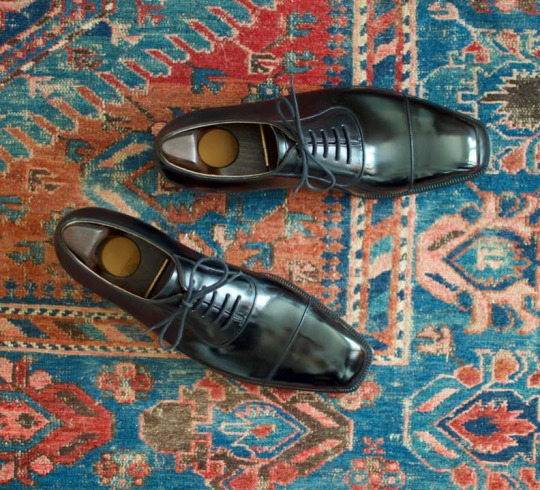
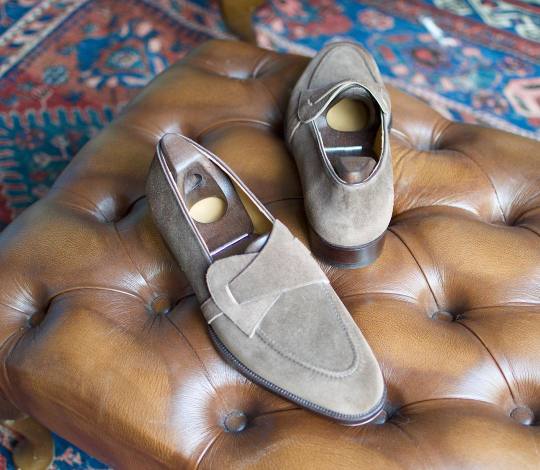
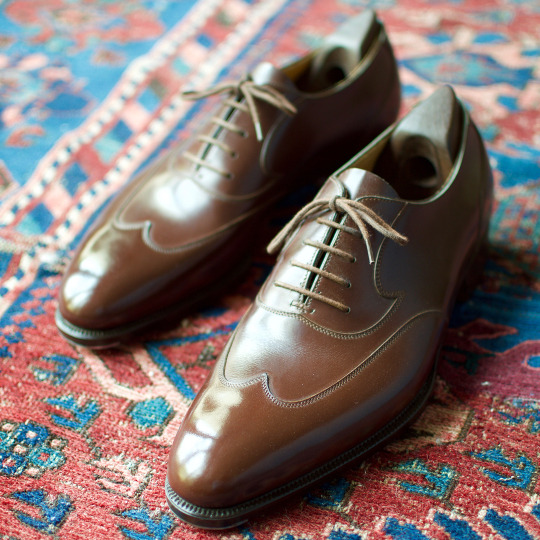
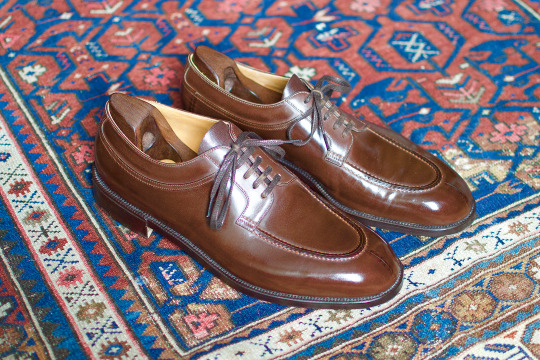
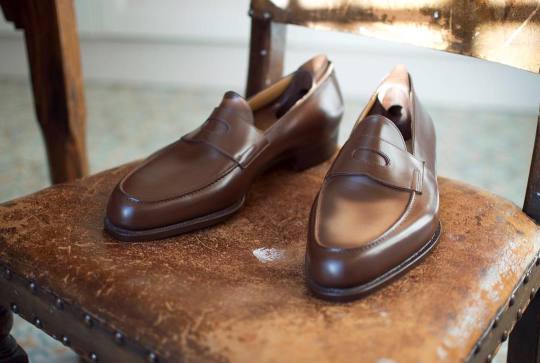
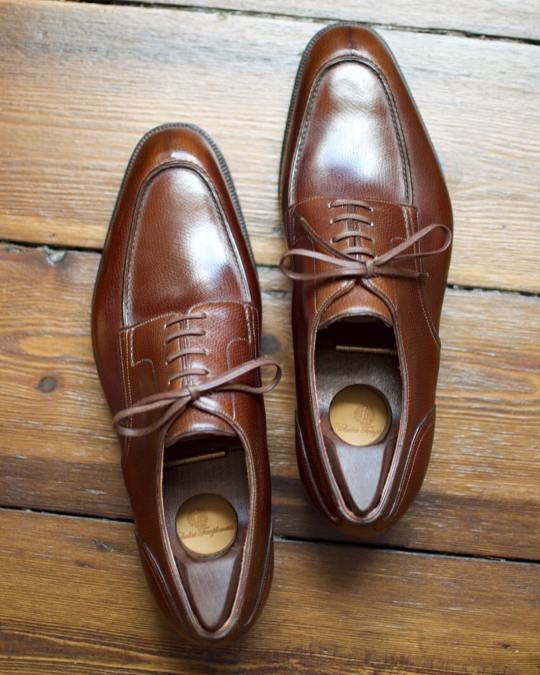
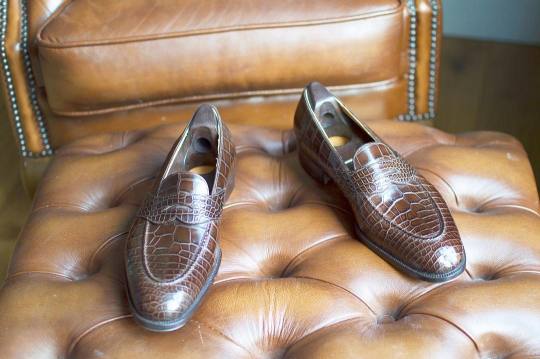
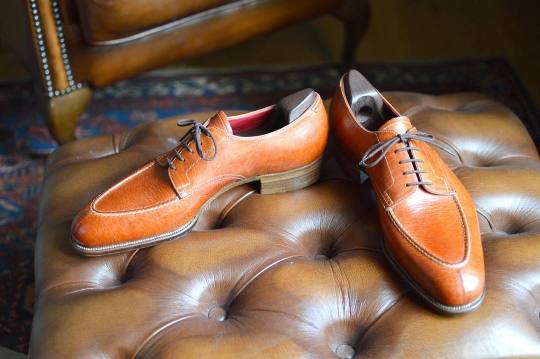
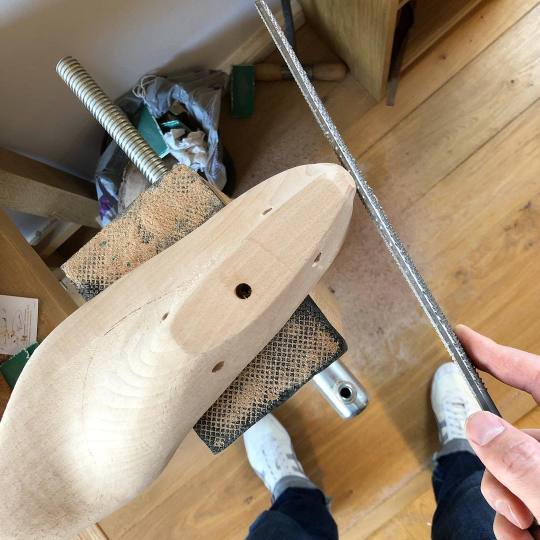
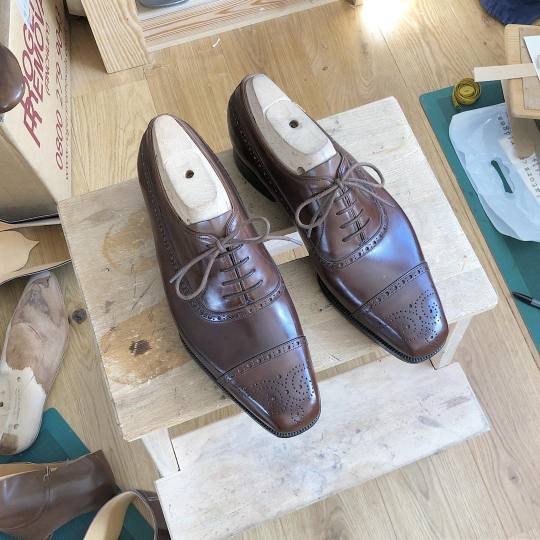
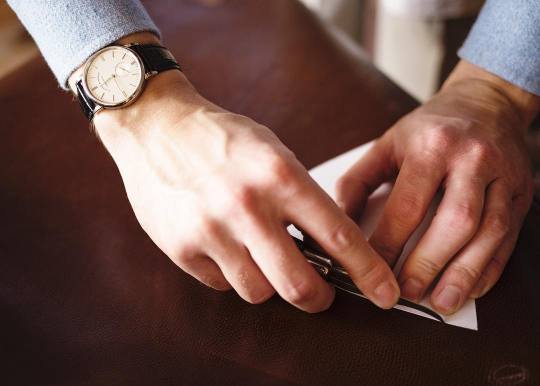
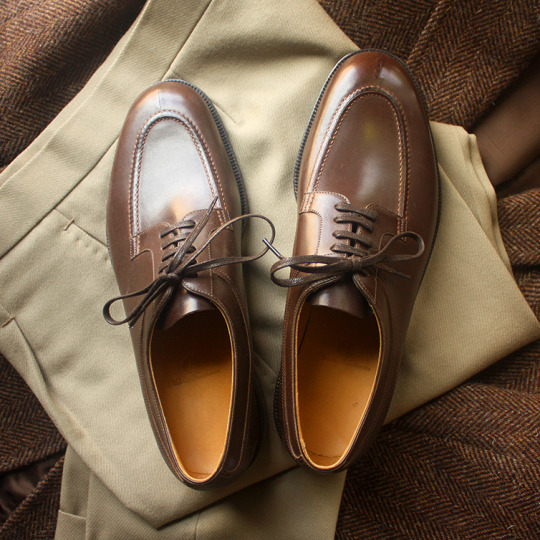
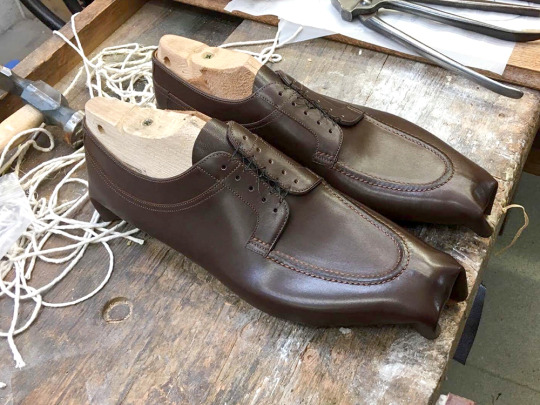
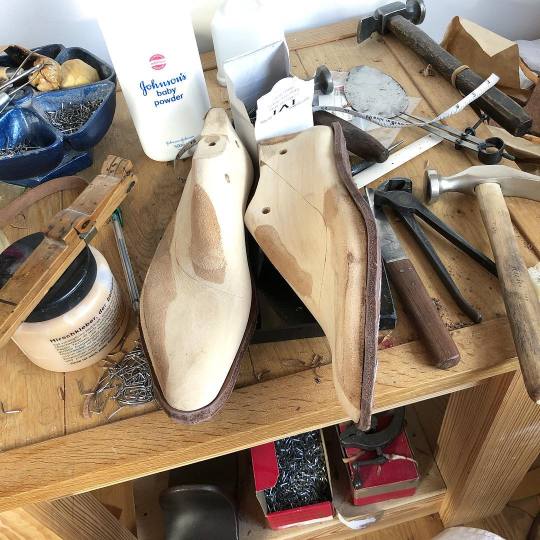
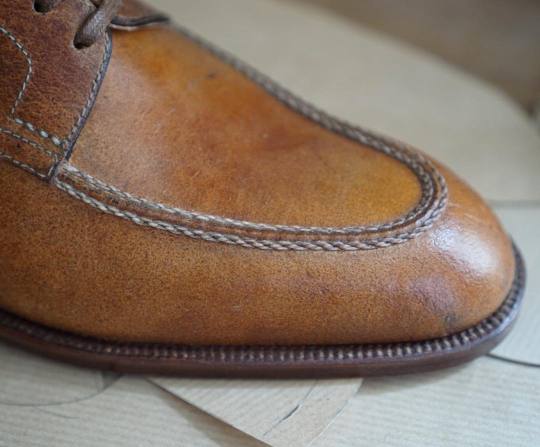
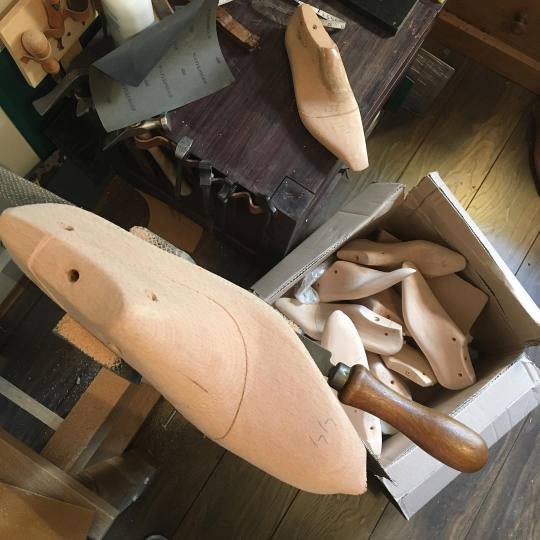
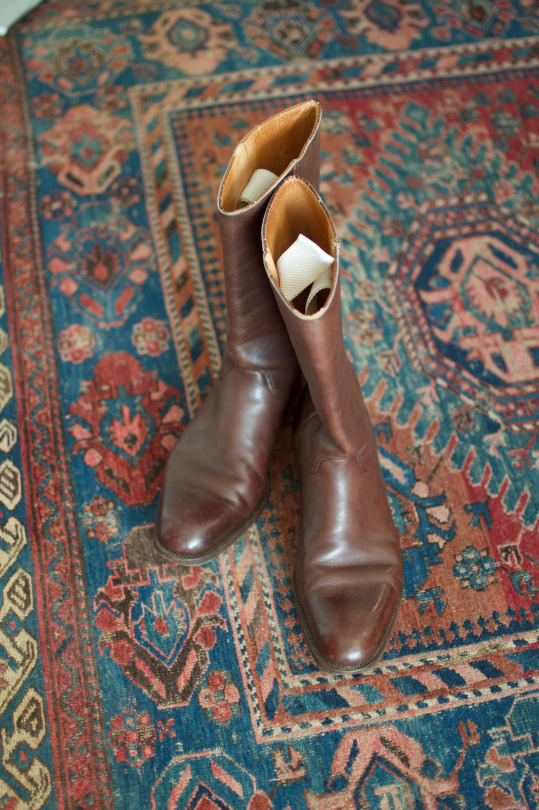
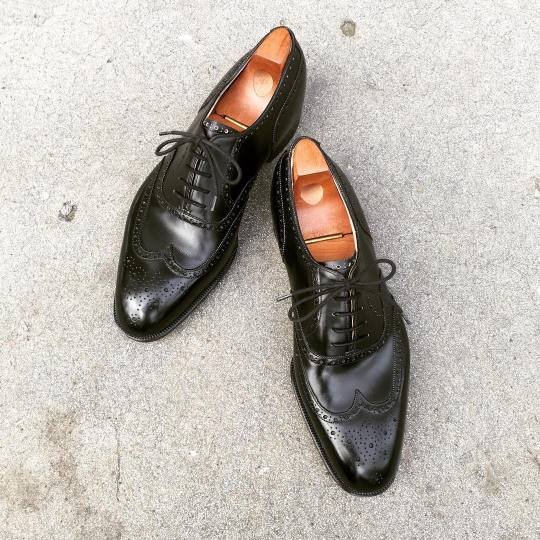
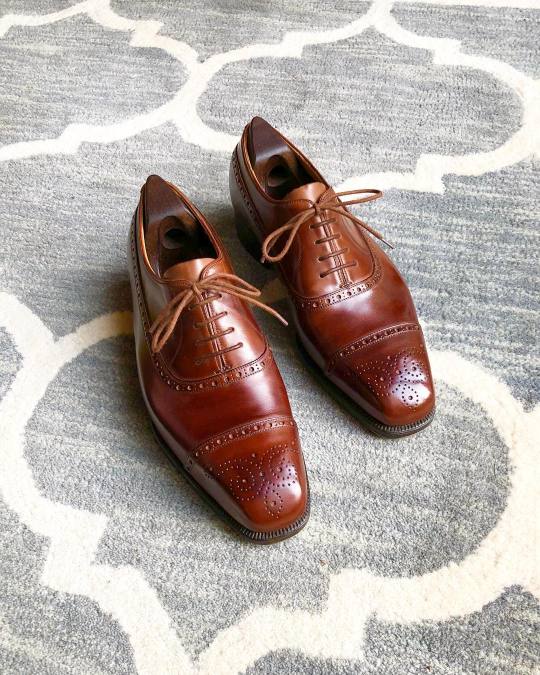